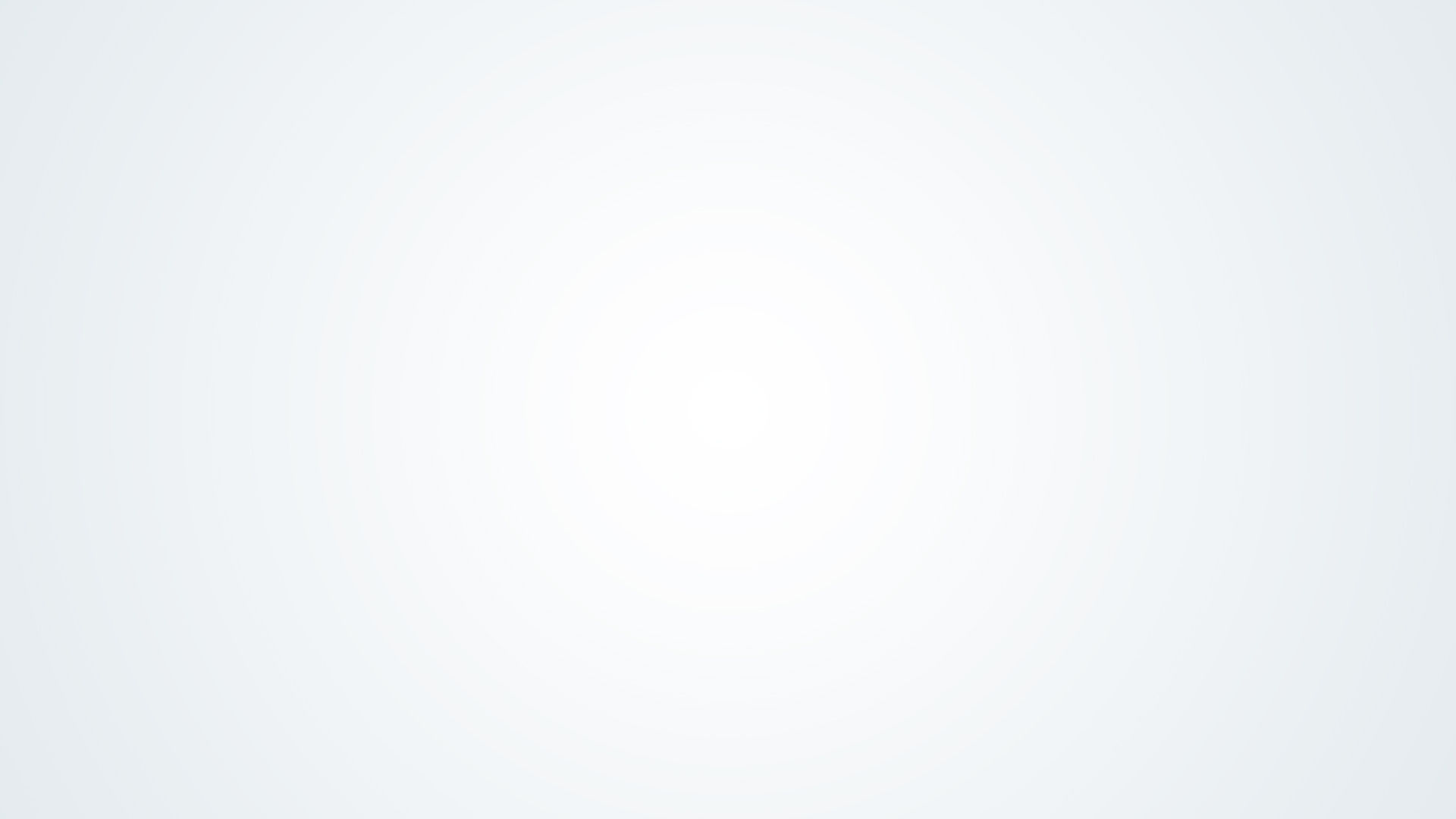
JAEMAN ALEX CHOI
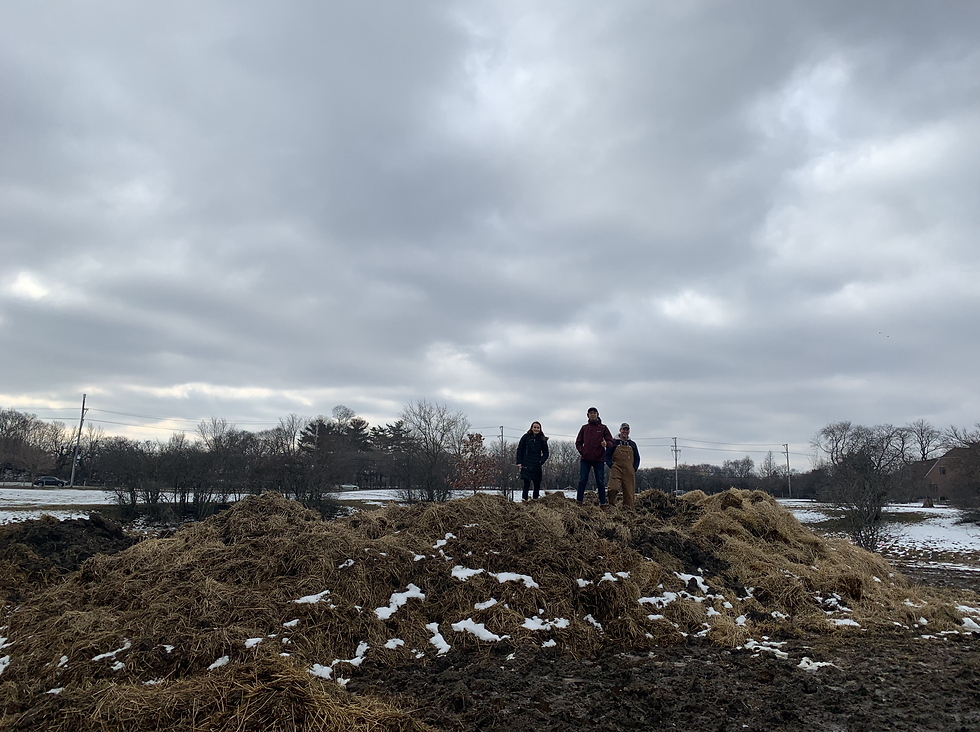
WAGNER FARM COMPOSTING:
AERATED STATIC PILE
WINTER 2020 -SPRING 2020
PROJECT OVERVIEW
20 WEEKS
This project stems from a 20 week intensive interdisciplinary Capstone Design Course where we were given a client in Wagner Farms. Mr. Kuerster and his farm needed a composting solution, and after initial site visit and extensive user and performance research we began to reimagine the system at Wagner Farms. In the first half of a two quarter long experience with four others, where we pulled on each others strengths and weaknesses, we delivered informative expert research and chemical testing in iterative fashion. After identifying the most important factors behind the inefficiencies of Wagner's current composting solution, we introduced the aerated static pile and a batch cycling method. With a minimal viable product to full scale of a single batch we were able to test and compile data on the efficiencies over the remaining weeks.
A detailed final report with aeration system calculations, FMEA analysis, cost analysis and more can be found here
PERSONAL RESPONSIBILITIES
-
Developed ideas through brainstorm and ideation sketching process
-
Informative interviews and research
-
Benchmark analysis and performance testing of current method
-
Professional Design Reviews
-
Building proof of minimal viable product: single full scaled batch aerated static pile system
SKILLS
Brainstorming &
Ideation Sketching

User Research

Rapid Prototyping
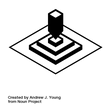
Injection Molding

BACKGROUND
Our Client
John Kuester
Wagner Farms

Our client John, runs Wagner Farms located in Glenview, IL. He has been operating a profitable local farm with plans of expansion. His establishment is truly unique, a blend of gritty work scene and a symbolic heritage center, with a splash of 1820s vibe.
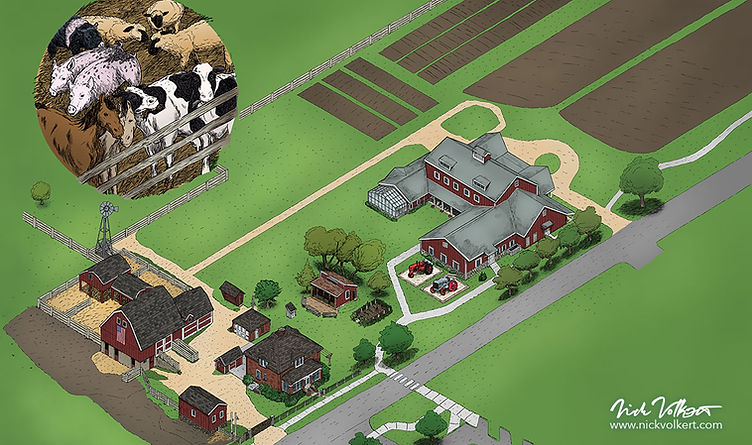
Executive Summary
Adequate oxygen, along with heat and moisture, turns even livestock waste to nutrient-rich compost within a few months. Our proposed three-pile system composts Wagner Farm’s 50-50 manure-straw waste more efficiently by introducing air through a pipe system beneath the pile. This method, known as aerated static pile composting (ASP), eliminates the need for laborious “turning” or mixing the pile to aerate.
Wagner Farm currently pushes waste into one large pile over the year, which can grow up to 60 tons, and has three dedicated farmhands load and turn the pile for 6 hr/wk using a skid-steer loader. The primary pile Wagner Farm creates is not only difficult to manage but inefficiently and unevenly creates compost over 6-12 months, making it ill-suited to spread on their fields for crop growth. Additionally, the farm’s proximity to residential Glenview, IL sets high standards for appearance and odor.
PROBLEM
Addressing the problem required research, chemical testing, informative interviews, and application of feedback during a nonstop iterative process.
Design Requirements
The six key requirements for our composting system are:
Size
The height must be < 12 ft to be accessible to the Bobcat. State water reclamation laws set an impermeable area (asphalt, concrete, etc material that does not allow water through) limit of 125 sq. ft [1]. The final design ideally minimizes any area used.
Performance
The system must fully compost the manure/straw mixture in < 6 months (current minimum time for composting).
Capacity
The system must be able to process over 5,000 kg/wk and 7 m3/wk inputs and store up to 55,000 kg (78 m3) compost at any given time to match the manure and straw produced.
Odor
The solution must contain or disperse the odor so that it cannot be detected from 10 ft away (distance to nearest path).
Usability
The solution must contain a mechanism, preferably integrated with current farm equipment, which allows users to load and unload in < 6 hrs/wk (current time spent).
Aesthetics
As a frequently visited heritage center in the Glenview residential district, the system must have a pleasant, historically appropriate appearance consistent with the rest of the farm.
The main objective beyond all else was to expedite the composting process, limit anaerobic decay and encourage efficient decomposition. As shown in the figure below, the brown pile in the current layout - due to the bobcats ability to navigate under the condition of the pile - received almost no aeration and chemical tests prove less moisture content and lower temperature. Meanwhile the yellow portions of the pile was turned every one to two weeks; the orange pile is intermediate, around three to four week rate of aeration.
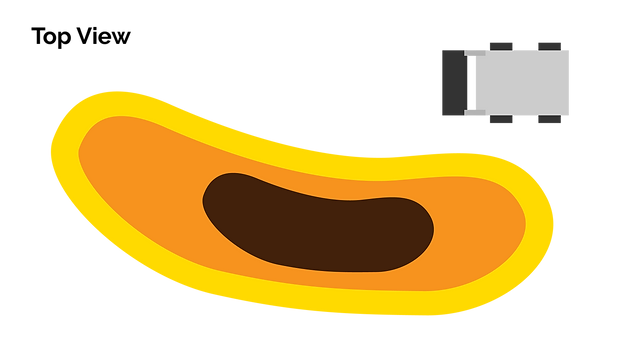
SOLUTION
To arrive at our solution it took a whole iterative process. Below are simple statistics of the measures we took.
5
Brainstorms
4
Interviews
(Client + Experts)
3
Mock ups
4
Presentations
(Peers + Experts + Client)

Design Concept
An aerated static pile uses a piping system connected to an air pump to push air out through the compost pile and into a bio-filter layer. This layer is a “finished” or fully composted pile, which acts as a carbon filter for the odor. Additionally, a mesh and wood chip layer sits between the pipes and manure to prevent particulate from entering the system. We implemented a drainage system with gradient and a pump to cycle the leachate back, for accessible maintenance. Compost is split up into 5 batches each distinct by their stage in the composting process. Finally, waterproof and tear resistant tarps insulate the piles from the elements while also having an aesthetic consistent with the historical theme.

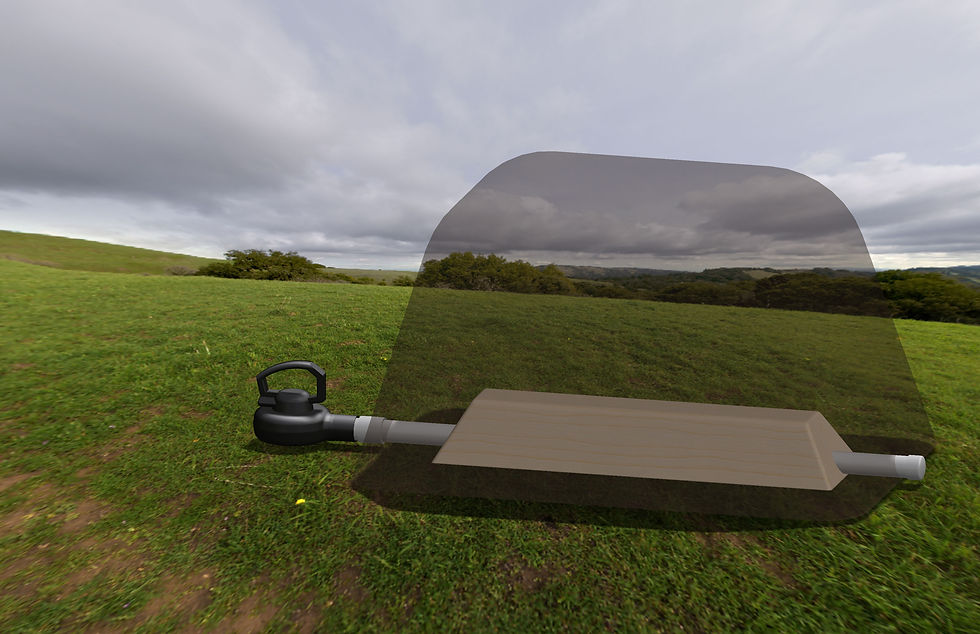


Minimal Viable Product & Testing (Single Batch Prototype)
Due to COVID 19, we adjusted the scope of our project to present a working MVP to our client supplemented with assembly instructions, testing procedure, and future directions. Here is a singular batch from our batch cycle concept illustrated in depth.


Wagner Farm assisted in conducting remote testing on the design concept. A half-height single batch size (8 ft x 10 ft x 5 ft) was constructed for this purpose. Other than the singularity, the system assembled mimicked the initial final design proposed. In the plot of land enclosed and nearest to the barn, as to use outlets, the system was assembled. A leaf blower of comparable CFM provided air through a single, perforated 10-ft PVC pipe with a 1ft layer of fresh wood chips, 4 ft mixture of manure and straw, and 1 ft layer of finished compost atop. A timer connected to the leaf blower set aeration time to 1 min on: 1 min off initially to match that needed for aerobic decomposition.
Wagner Farm staff monitored the pile daily, taking temperature measurements, writing down observations on pile moisture and compost appearance/smell, and documenting the process with videos and photos uploaded to a shared Google Drive. Along with assessing feasibility, this information has helped in developing solutions for the potential failure points determined in the FMEA analysis.
Future Directions
After having transitioned into a larger underground piping system with five respective centrifugal blowers, there is value in developing further components. Other than continued iterative testing of comparing ambient temperatures with the internal/external temperatures of the piles, there is much needed to be done to perfect the Wagner Farm composting system. Directions that future teams can take to expand upon the project are designing a system to collect and reuse leachate, optimizing energy use and cost, finding a better covering or weatherproofing option